
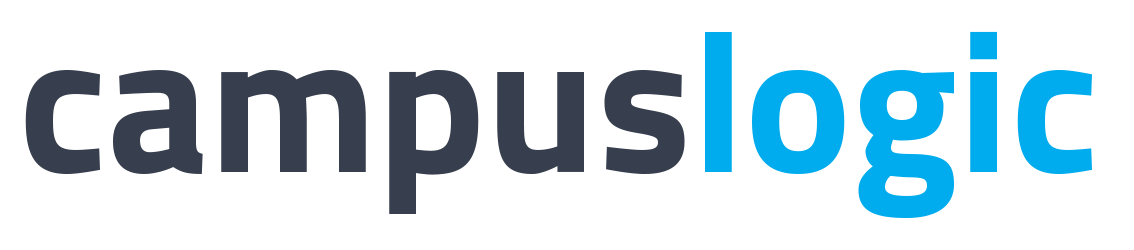
Molecular dynamics (MD) simulations that explicitly model the mechanical metamaterial 17 show a stiffness over one order of magnitude smaller than that of its softest component.

We note that stiffness depends on microstructure (via texture), but to a much lesser degree than strength and toughness, and can to date only be engineered to a large extent via open structures such as foams and lattices, which incorporate air as a second phase. In this paper, we use theory to design an ultra-low stiffness metamaterial, a composite that defies the constraints of the rule of mixtures for a quasi-static property weakly sensitive to microstructure: stiffness. Even the recent, remarkable observation of stiffening of a solid via nanoscale liquid inclusions can be explained by classic composite theory after the incorporation of interfacial tension 16. We mentioned that the weighted average rule applies exactly to density and has, to date, provided inexorable bounds on stiffness. Intrinsic properties have proven more challenging. Examples include biomimetic composites with high toughness 13, 14 and composites designed for low thermal conductivity 15. Breakthroughs in materials science and engineering have enabled overcoming such constraints for extrinsic properties, those that depend strongly on microstructure. There is significant interest in breaking rule of mixtures constraints to reach otherwise unachievable properties. This is true even as composite, foam, and lattice material design has successfully filled previously inaccessible materials property space 8, for example, ultra-low stiffness metallic micro-lattices 9, 10 and structures with negative Poisson’s ratio 11, 12.
#Purdue ces edupack series
Such properties are bounded by extrema obtained by the addition of phases in series or in parallel. Properties like stiffness depend on the arrangement of phases and elegant solutions exist for simple geometries 7. The weighted average rule applies rigorously for properties like density where the value for the composite can be obtained as a sum over phases: ∑ x i ρ i where x i is the volume fraction of phase i and ρ i its density. With few notable exceptions, their properties fall between those of its constituents and various forms of the rule of mixtures play a central role in composite design.
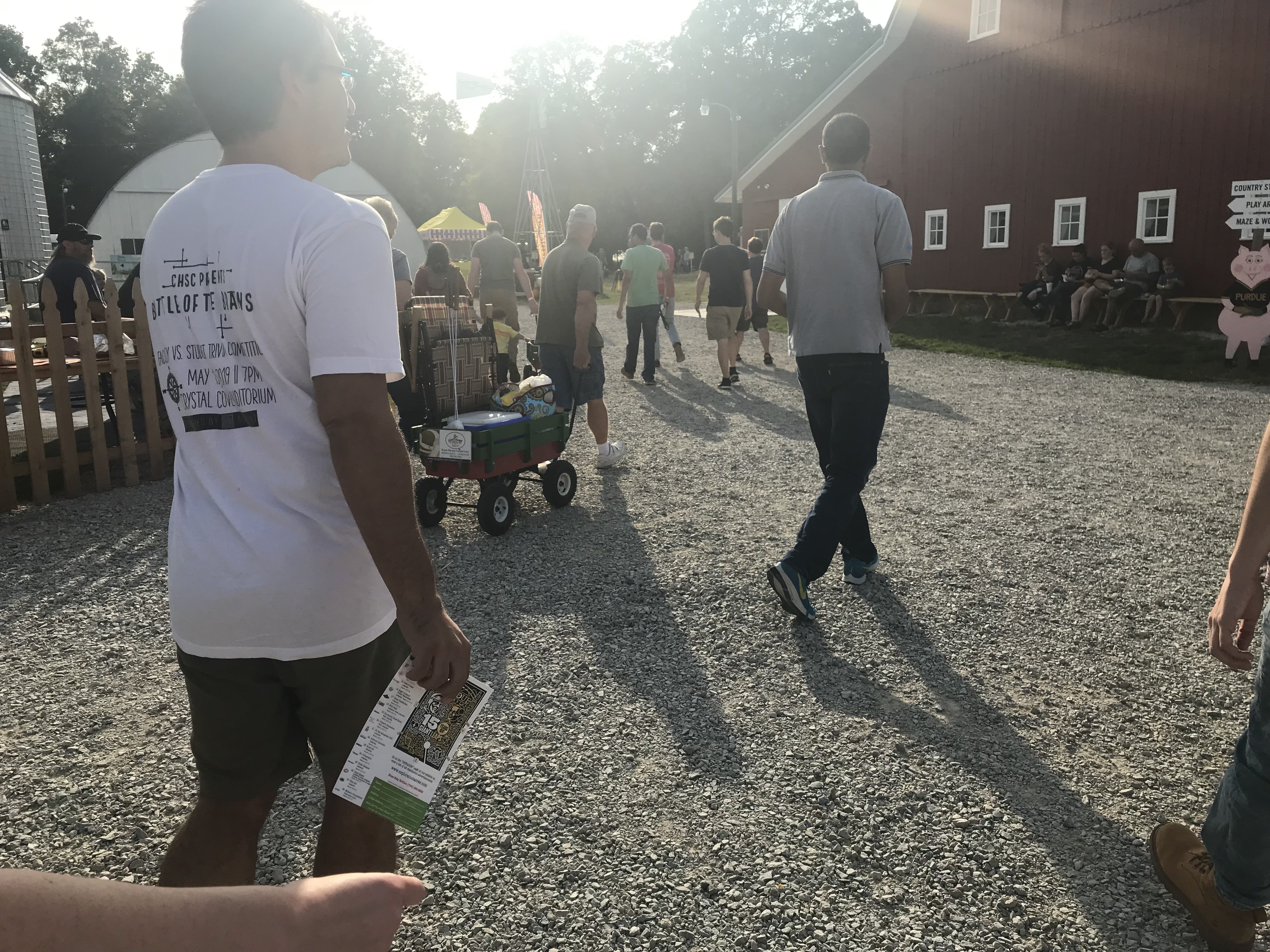
Unfortunately, the design of composites is not without limitations. Nature also uses composites to achieve outstanding mechanical performance by arranging relatively humble materials in optimized microstructures 3 classic examples include nacre 4, bone 5, and spider silk 6. Our concept is generally applicable and could significantly enhance materials science design space.Įngineered composites combine distinct materials to achieve properties or processability not available in the individual components and find widespread use, from advanced airframes 1 to biomedical implants 2. Such properties are attractive for flexible electronics and implantable devices. We find moduli as low as 2 GPa, a value typical of soft materials and over one order of magnitude lower than either constituent, defying long-standing composite bounds.
#Purdue ces edupack full
Explicit large-scale molecular dynamics simulations of the metamaterials with state of the art potentials confirm the expected ultra-low stiffness while maintaining full strength. Here we design ultra-low stiffness in fully dense, nanostructured metals via the stabilization of a mechanically unstable, negative stiffness state of a martensitic alloy by its coherent integration with a compatible, stable second component. This is because stiffness is insensitive to microstructure and bounded by individual components in composites. Alloy and microstructure optimization have led to impressive improvements in the strength of engineering metals, while the range of Young’s moduli achievable has remained essentially unchanged.
